AFO034 Oil Filtration System For The Transformer Oil Oil Purification System
Impurities: <1μm
Work pressure: 0.6~1Mpa
Payment Terms: TT , LC , Others
Payment Terms: TT , LC , Others
Oil filtration systems are specialized equipment used to remove impurities and contaminants from various types of oils, including lubricating oils, hydraulic oils, transformer oils, and more. These systems are designed to maintain the cleanliness and quality of the oil, thereby enhancing the performance and lifespan of the equipment or machinery that relies on it.
Applications
Oil filtration systems find applications in various industries, including automotive, manufacturing, power generation, aerospace, and more. They are used to maintain the cleanliness of oils in engines, hydraulic systems, turbines, transformers, and other equipment.
By employing effective oil filtration systems, industries can reduce equipment downtime, improve operational efficiency, extend the lifespan of machinery, and minimize the risk of costly repairs or replacements. The specific design and features of an oil filtration system can vary depending on the intended application and the requirements of the oil being filtered.
Features
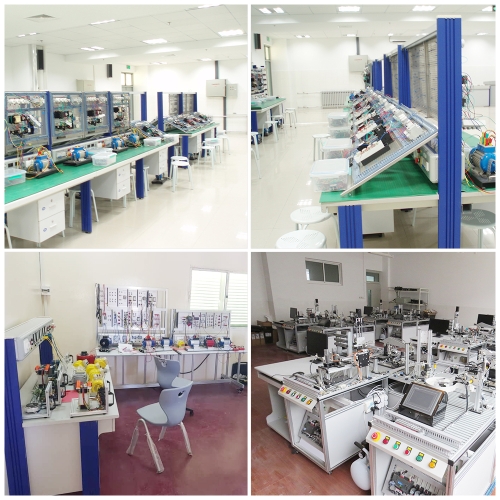
AirYa oil filtration systems use the centrifugal separation method, has the following advantages:
High Efficiency: Centrifugal separation is highly efficient in removing solid particles and water from oil. It can effectively separate and collect contaminants of various sizes, ranging from large particles to submicron-sized particles. The centrifugal force generated during the process allows for efficient separation, resulting in clean oil.
Continuous Operation: Centrifugal separators can operate continuously, allowing for uninterrupted filtration and purification of oil. They can handle a continuous flow of oil without the need for frequent stoppages, making them suitable for applications that require continuous operation and minimal downtime.
Fast Processing: Centrifugal separation is a relatively fast method for oil filtration. The separation process occurs within a short period, allowing for quick turnaround times. This is particularly advantageous in industries where time-sensitive operations are involved.
Scalability: Centrifugal separators are available in various sizes and capacities, making them suitable for a wide range of applications. They can be scaled up or down to accommodate different flow rates and volumes of oil. This scalability allows for flexibility in implementing centrifugal separation in various industries and applications.
Reduced Maintenance: Centrifugal separators generally have fewer moving parts compared to other filtration systems, which leads to reduced maintenance requirements. They are designed for reliable and long-lasting operation with minimal wear and tear. This helps to minimize maintenance costs and downtime associated with system maintenance.
Versatility: Centrifugal separators can be used for different types of oils, including lubricating oils, hydraulic oils, transformer oils, and more. They are suitable for a variety of industries such as manufacturing, power generation, automotive, marine, and aviation. The versatility of centrifugal separation makes it a widely applicable method for oil filtration and purification.
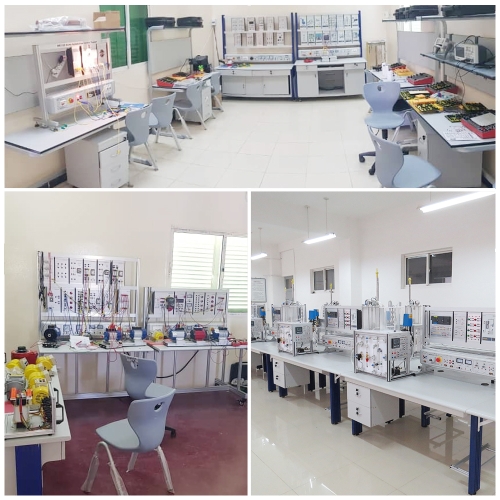
Extend Equipment Life: By efficiently removing contaminants from the oil, centrifugal separation helps to protect equipment and machinery from premature wear and damage. Cleaner oil with reduced particle contamination can extend the lifespan of critical components, such as bearings, gears, and seals, resulting in improved equipment reliability and reduced maintenance costs.
The most important point is that there is no need for high temperature heating, no damage to the oil and the filtered oil can reach the quality of new oil.
The importance of transformer oil filtration
Oil filtration systems play a critical role in maintaining the performance and reliability of transformer oil in electrical power systems. Transformer oil, also known as insulating oil, is responsible for insulating and cooling the transformer's core and windings. Over time, transformer oil can become contaminated with moisture, particulate matter, and chemical byproducts, which can degrade its insulating properties and affect the transformer's efficiency and lifespan. Here is a professional perspective on the role of oil filtration systems for transformer oil:
Contaminant Removal: Transformer oil can accumulate various contaminants during its service life, including moisture, dissolved gases, particulate matter, and oxidation byproducts. These contaminants can affect the oil's dielectric strength, thermal conductivity, and lubricating properties. Oil filtration systems, such as high-efficiency particulate filters, coalescers, and vacuum dehydration units, are designed to remove these contaminants,ensuring that the oil remains clean and free from harmful particles that could compromise the transformer's performance.
Sludge and Varnish Removal: Over time, transformer oil can develop sludge and varnish deposits due to oxidation and thermal degradation. These deposits can coat the transformer's windings and affect heat dissipation, leading to increased temperatures and accelerated aging of the insulation system. Oil filtration systems with suitable filtration media and adsorbents can effectively remove sludge, varnish, and other degradation byproducts, ensuring clean oil and preserving the transformer's operational efficiency and lifespan.
Insulation Preservation: The insulation system in transformers is critical for maintaining electrical integrity and preventing failures. Clean and well-maintained transformer oil is essential for preserving the insulation materials. Oil filtration systems play a crucial role in removing contaminants and preserving the oil's dielectric strength, thereby extending the life of the transformer's insulation system and minimizing the risk of electrical faults.